TG 9: Additive Manufacturing
Additive manufacturing has known an increasing interest in recent years because of its capability to create complex shapes with limited amount of subsequent material removal. Powder metallurgical techniques or successive weld bead deposition have opened up additive manufacturing principles also for the production of metallic components. This renders it conceivable that additively manufactured components could also be suitable for nuclear applications, if research can demonstrate that the corresponding performance requirements are met.
In Task Group 9, an experimental setup has been designed to investigate the influence of process parameters during the Wire Arc Additive Manufacturing process (WAAM). This experimental study has been also designed as a WAAM benchmark for numerical investigations such as thermal–mechanical ones (1).
Sample preparation for the TG 9 studies consisted in the deposition of 5 successive layers of 316L stainless steel filler-wire on the edge of a base plate (124x50x6mm). This configuration can be assimilated to a 2D configuration exhibiting a case of plane stresses. 3 different sets of process parameters were implemented based on variations of travel speed and linear energy depositions ranging from 147.1 to 189.7 J/mm. Set 1 and 3 have almost the same linear energy but different process parameters (voltage, current and travel speed). Set 2 has the highest linear energy with a higher wire feed speed and therefore higher welding current. Table 1 shows the details of the three parameter sets.
The welding thermal cycle was clearly visible on the time evolution of the displacement of the base plate corner, also varying cyclically by a few tenths of a millimeter, as well as on the weld pool size (2). The weld pool size increased (up to 5 mm) with the number of beads increasing since the temperature of the specimen increased in the course of the deposition process.
Measurements such as welding current and voltage, temperature, weld pool images and local displacement have been performed in-situ to provide input data for subsequent numerical analyses of the process. Other measurements have been realized ex-situ, such as micro-structure and residual stress determinations. To date, residual stresses have been investigated by the neutron diffraction technique on two specimens. The effect of varying process parameters on the residual stresses in the fusion zone has been moderate, but it has still been possible to show it in these investigations.
Table 1: Details of the three process parameter sets
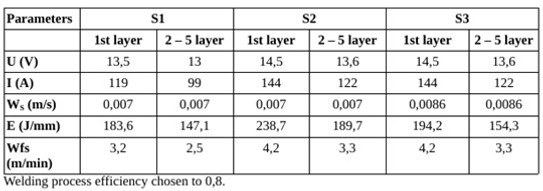
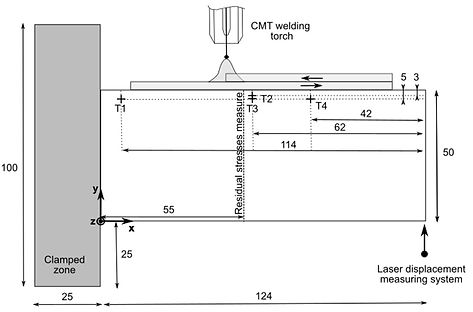
Figure 1: Sketch of the specimen production: the base plate is held vertically with the weld bead deposition made along its long edge. The position of the thermocouples is indicated by «T» followed by numbers from 1 to 5. Residual stress measurements were made along the central vertical line.

Figure 2: Time evolution of the temperature at thermocouple T2 and displacement of a free corner of the base plate during the 5 thermal cycles followed by cooling.

Figure 3: Electron Back-Scattering Diffraction pattern across all 5 beads in the middle of the specimen produced according to process parameter set S3.

Figure 4: View of the weld pool at different moments with a high speed camera. The process parameter set S2 was used here.

​Figure 5: Comparison of longitudinal stresses measured by neutron diffraction at 3 different facilities along the middle line (Fig. 1) through the substrate and the weld beads (the latter are between 53 and 63 mm). A specimen produced with process parameter set S2 was used here.

Figure 6: Map of welding longitudinal residual stresses in a specimen produced with process parameter set S2. The neutron diffraction measurements were performed at the ILL, Grenoble, France.
References
-
C. Cambon, S. Rouquette, I. Bendaoud, C. Bordreuil, R. Wimpory, F. Soulié, Thermomechanical simulation of overlaid layers made with wire + arc additive manufacturing and GMAW-cold metal transfer, Weld. World 64 (8) (2020) 1427–1435.
-
C. Cambon, I. Bendaoud, S. Rouquette, F. Soulié, A WAAM benchmark: From process parameters to thermal effects on weld pool shape, microstructure and residual stresses, Materials Today Communications vol 33 (2022).
​
​